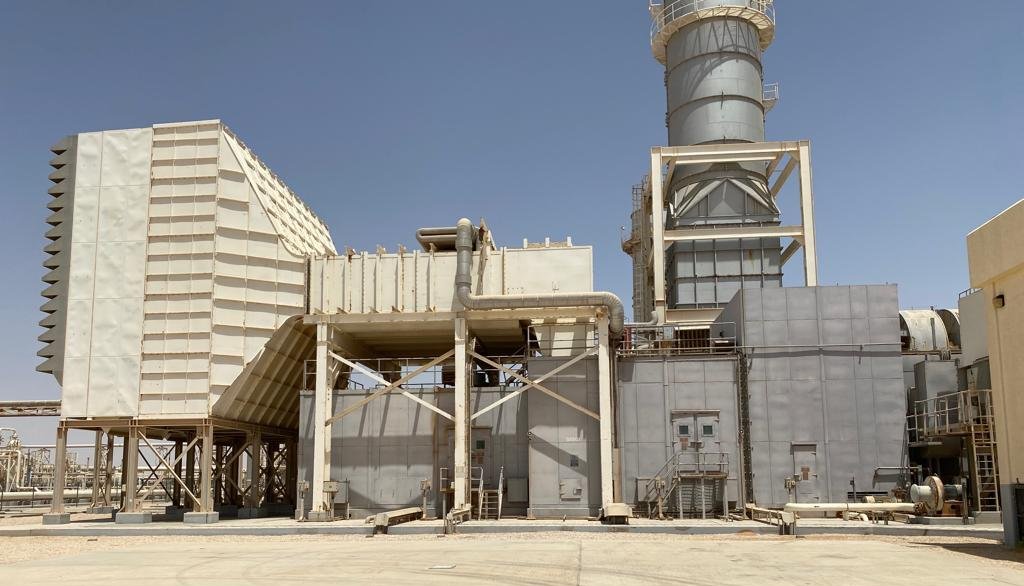
A combined-cycle power system typically uses a gas turbine to drive an electrical generator, and recovers waste heat from the turbine exhaust to generate steam. The steam from waste heat is run through a steam turbine to provide supplemental electricity. The overall electrical efficiency of a combined-cycle power system is typically in the range of 50–60% — a substantial improvement over the efficiency of a simple, open-cycle application of around 33%.
A combined-cycle power system is the traditional technology of choice for most large onshore power generation plants, and is therefore well established. The technology have also been used on a few offshore installations for over 10 years. Most offshore installations are designed to generate power from open-cycle gas turbines which offer reduced capital costs, size and weight (per MW installed), but with compromised energy efficiency and fuel costs per unit output. Combined-cycle system operation is suitable for stable load applications, but less suitable for offshore applications with variable or declining load profiles. In a new ‘greenfield’ development incorporating a combined-cycle system design, the size of the gas turbine can be optimized and is likely to be smaller than an equivalent open-cycle configuration. Additionally, the waste heat recovery unit (WHRU) can replace the gas turbine silencer, thereby mitigating some of the space and weight constraints. Residual heat may be used instead of fired heaters, thereby improving the overall system efficiency. As such, the use of combined-cycle power technology is dependent on the power and heat demand of the installation. Combined-cycle technology is most cost-effective for larger plants. On an installation where the heat demand is large, the waste heat from the WHRU will normally be used for other heating applications, and hence there will be little residual heat left for power generation.